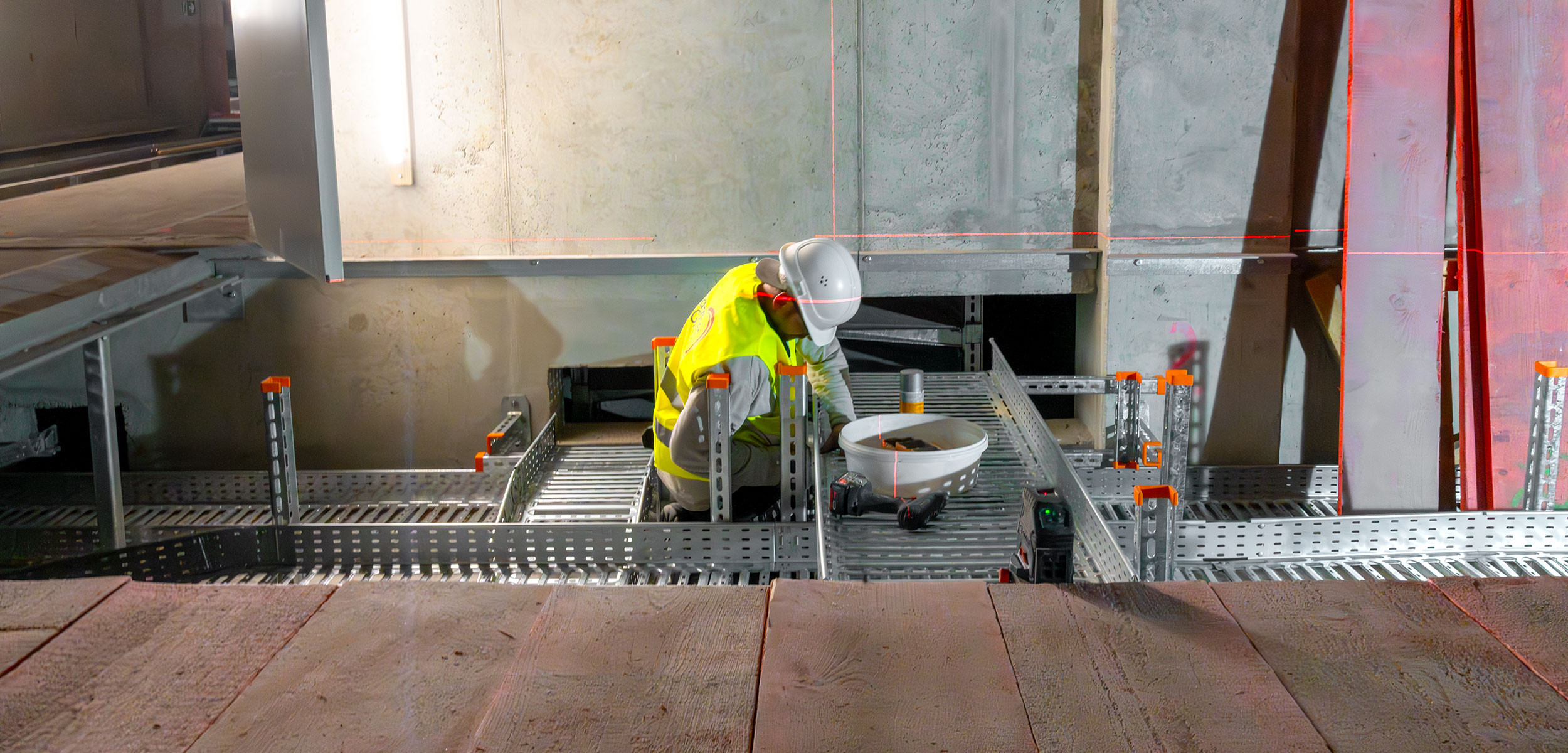
Aiming high: Challenging projects at Munich Airport
Tray construction and telecommunications engineering for the extension of Terminal 1
We are proud to be able to look back on a long and trusting cooperation with the Munich Airport: Our expertise in electrical engineering was in demand for several decades, even at the former location in Munich Riem. The new Munich Airport has grown steadily since its opening in 1992.
Profile
Order
Expansion of Terminal 1 at Munich Airport
Period
- April 2023 – September 2024 (tray construction)
- July 2023 – July 2025 (communications engineering)
Interesting figures communications engineering
- Approx. 110 pieces of network and marshaling distributors 42RU
- Approx. 400 pieces of CU small distributors (TSAV)
- Approx. 50 pieces of fiber optic small distributors
- Approx. 80 pieces of FOC 3U sub-racks
- Approx. 500 pieces of slide-ins for 3RU sub-racks
- Approx. 50 pieces splice housings
- Approx. 1,000 SSS Plus mounting trays
- Approx. 10,000 SSS Plus separation strips
- Approx. 2,000 pieces of RJ45 patch cables
- Approx. 10,000 pieces of two-wire switchings
- Approx. 6,000 pieces of fusion splices
- Approx. 5,000 pieces of data ports
- Approx. 12,000 pieces of cable markers
- Approx. 1,500 m of cable trays and mesh trays
- Approx. 10,000 m of pipes
- Approx. 2,500 m of earthing cables
Developer
Flughafen München GmbH
Project description
Terminal 1 is currently being expanded to include a new pier, which, including the entrance and exit area in Module B, has a total area of 95,000 square meters. It will create additional space for six wide-body or twelve smaller aircraft. This is where the Bachner Group comes into play: We have been commissioned to build the cable trays and provide the telecommunications engineering for the extensive expansion of Terminal 1.
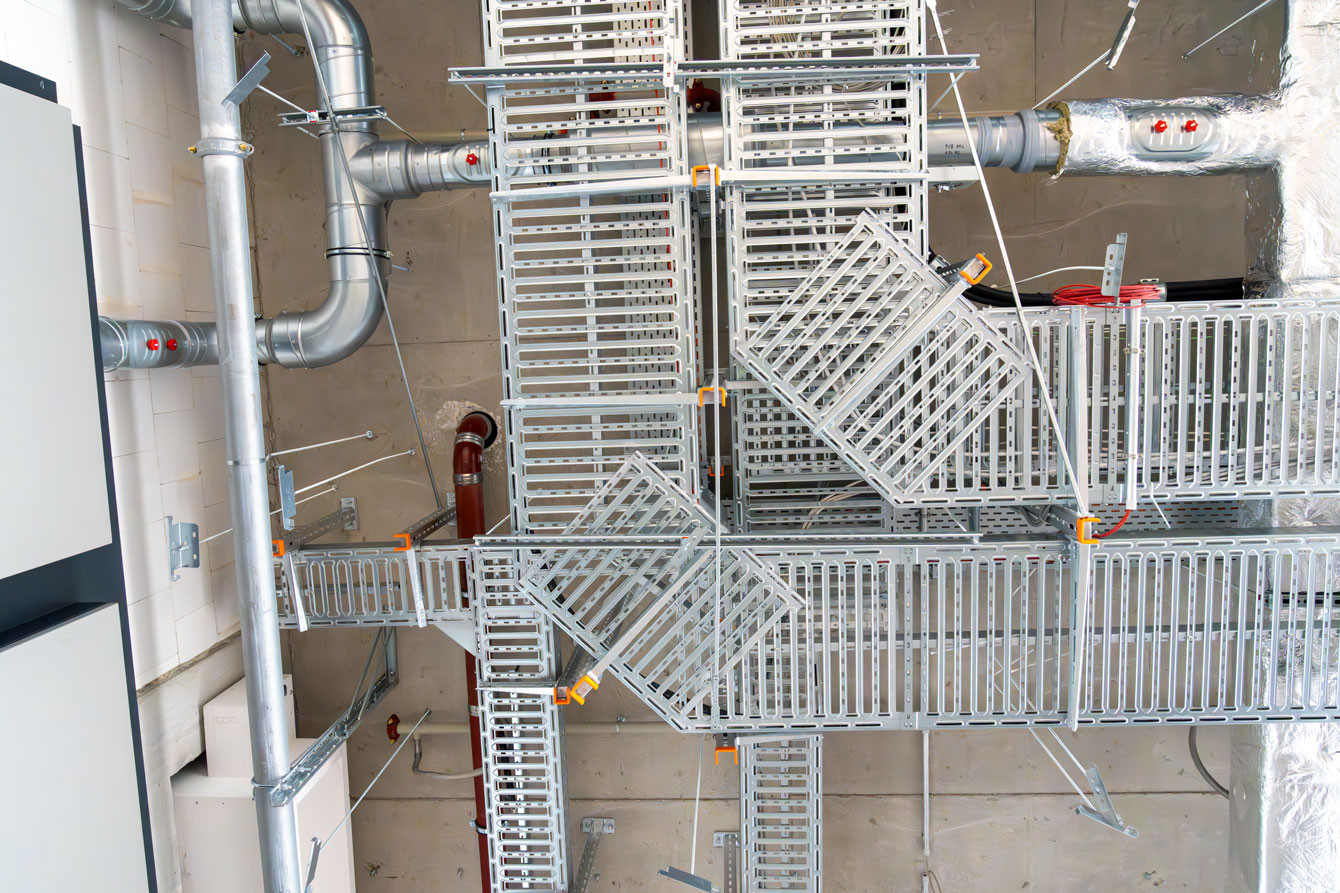
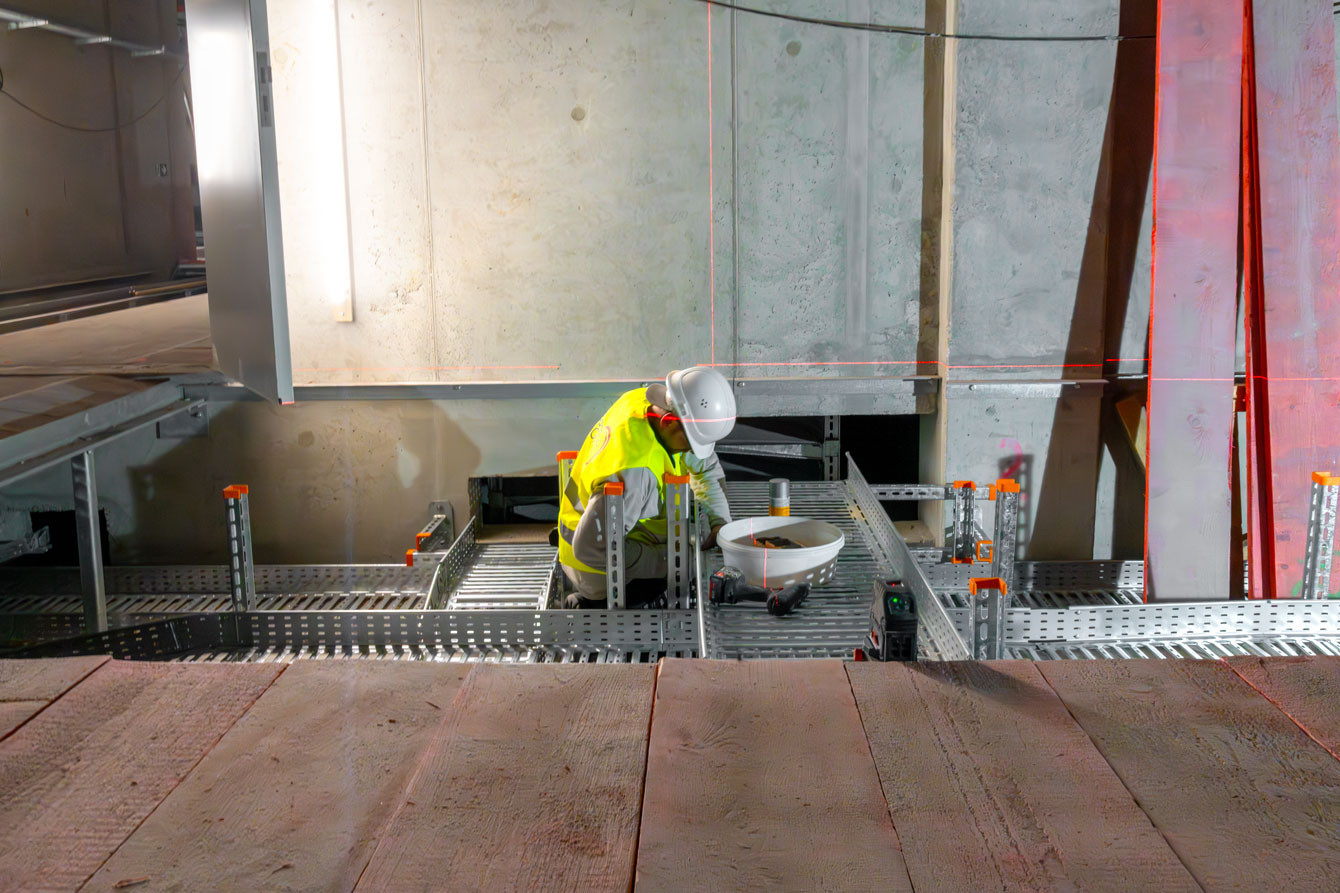
Cable trays are the foundation for supply
The tray construction project is progressing since April 2023 and it is supervised by two on-site project managers, Terence Woll and Simon Treffler. We have a comprehensive contract and are responsible for planning, execution, possible adjustments and the final handover. There are plenty of trays and troughs to be laid on six floors: In total, around 50 kilometers will be needed by the expected end of the project in September 2024.
Forward-looking planning is vital
However, the tray construction project presents a few challenges. Due to the large number of cables for energy, signal or frequency transmission required for the expansion of Terminal 1, the cable trays must be selected and laid accordingly. “The difficulty is that some of the trays are laid on top of each other so that the different parts of the building can be supplied,” says project manager Terence Woll. "However, due to the diameter of the individual cables and their sheer quantity, we have to ensure that the trays are kept at the right distance to each other - otherwise the cables will hit the tray above or not fit in at all."
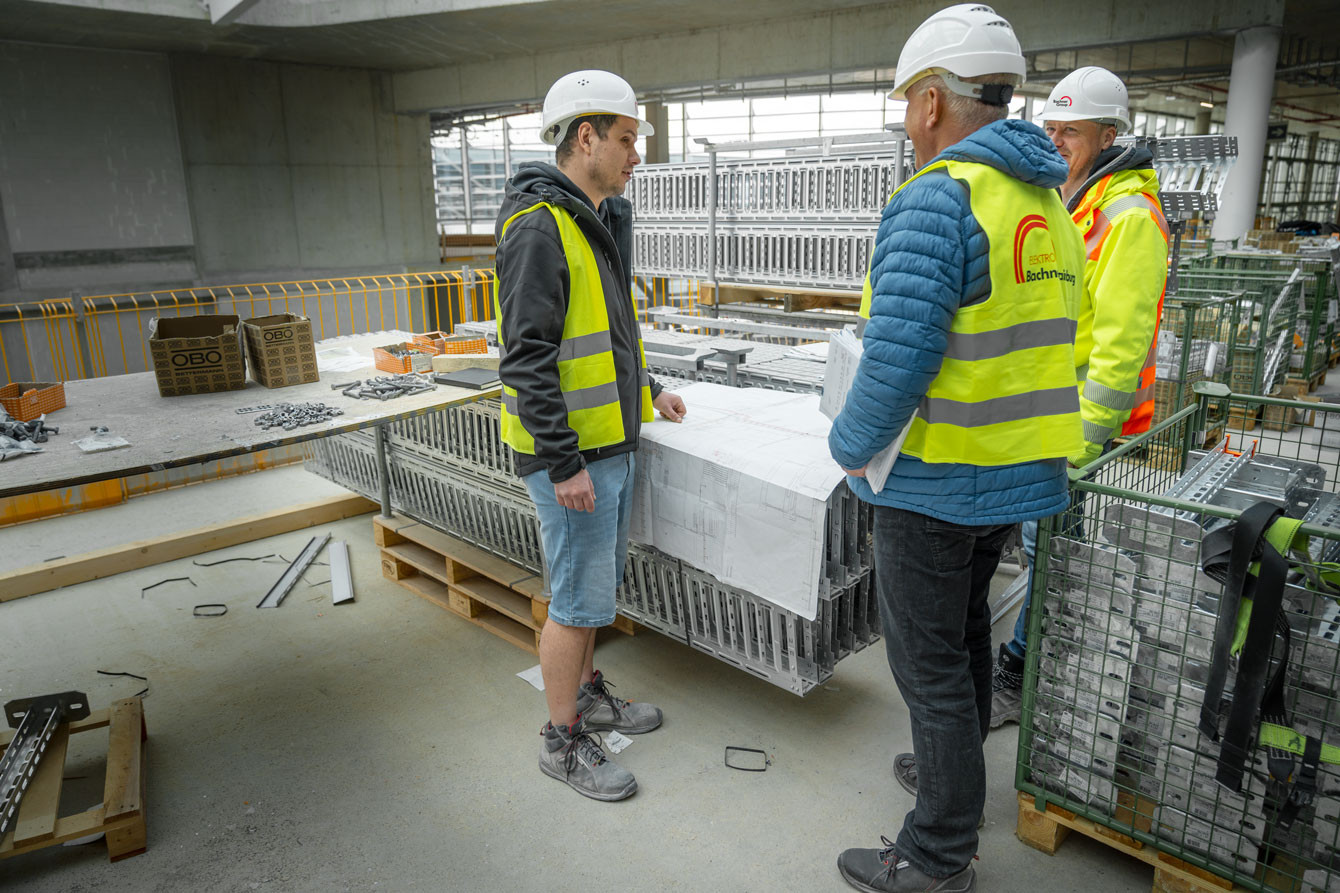
Full concentration on telecommunications engineering
Our Dingolfing colleague, Helmut Kiermeier, is responsible for the supply in the area of telecommunications engineering. Between July 2023 and July 2025, 50 distribution rooms will be equipped with floor trays, raised floors, mesh trays and distributors and the cables will be laid, connected and measured accordingly throughout the building. The main distribution room alone has impressive dimensions of 5.5 meters by 20 meters. In total, the extension will require around 35,000 meters of FOC, 300,000 meters of data cable and 100,000 meters of multi-pair cable.
The latter include a wide variety of types: from telecommunications cables with ten double wires (DA), to 20 DA and 50 DA, to those with 100 DA, everything can be found here. Concentration is particularly important when laying cables with 100 DA. “A cable with 100 DA consists of ten basic bundles and the counting bundle is marked in red. When laying the cable, it has to be determined whether it is an incoming or an outgoing cable,” explains project manager Helmut Kiermeier. Looking at the cable, outgoing multi-pair cables must be counted counterclockwise, while incoming cables must be counted clockwise. This requires full concentration!
All in all, the project is very complex. “Teamwork is important so that we always keep an eye on all overarching aspects – my colleagues from Dingolfing, especially my site manager Dimitar Kopanarov, are a great support here,” says Kiermeier.
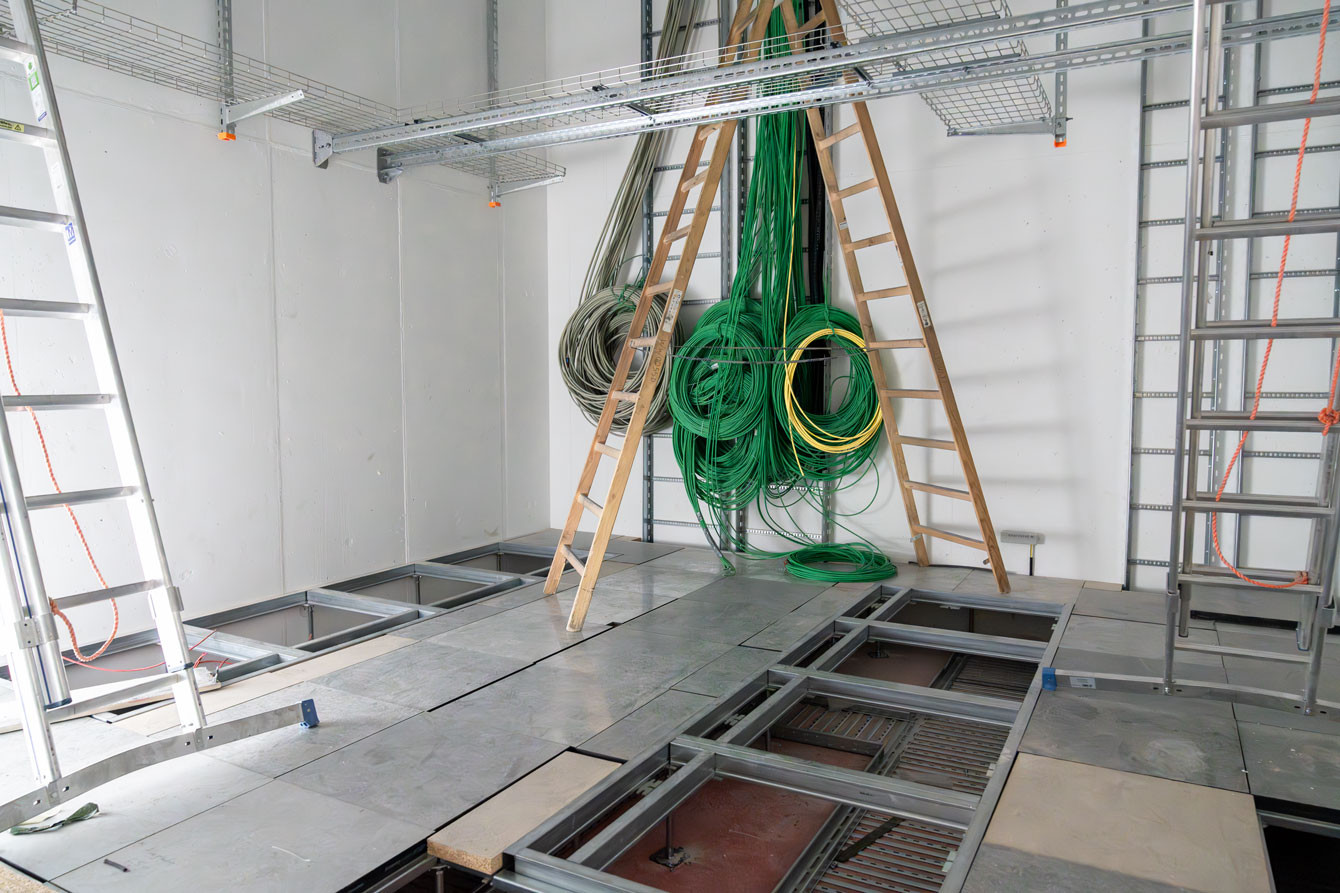
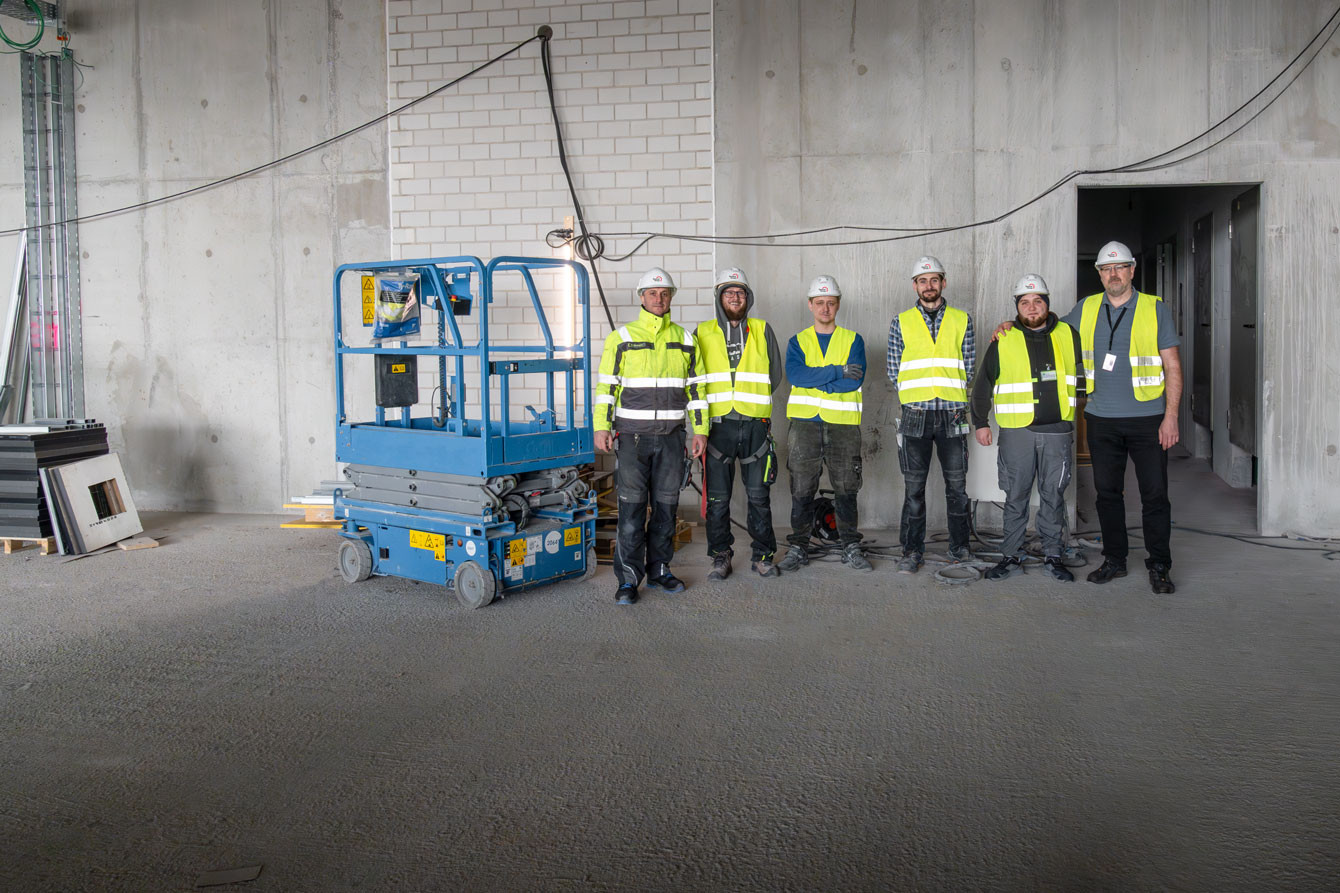
Safety first
The airport is a very exciting working environment – but it also brings with it some unique conditions. For our employees to gain access to the security area of Munich Airport, they must undergo a background check by the responsible aviation security authority. “However, this review takes time, so our colleagues have to wait for the approval before they can start working here. We therefore apply for the necessary documents as early as possible – this way there are no delays,” says department head Peer Uhlemann.
Things are moving forward!
Overall, the three project managers agree: there is a solid collaboration with the Munich Airport. There is an interest in having all open questions clarified so that the tasks at hand can be completed. This makes the work much easier and nothing stands in the way of comprehensive trial operations in 2025. With the extension of Terminal 1, passengers will not only be able to access arrival and departure areas as well as security and passport controls, but also high-quality retail stores and restaurants. We are excited to see what the finished building will look like and look forward to future cooperations with the Munich Airport.